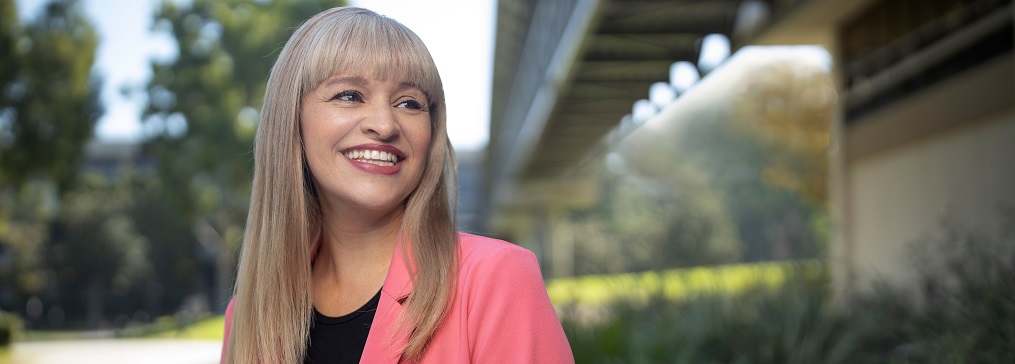
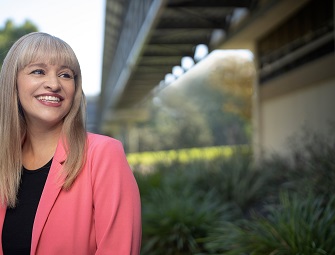
CONQUER BY IMPROVING.
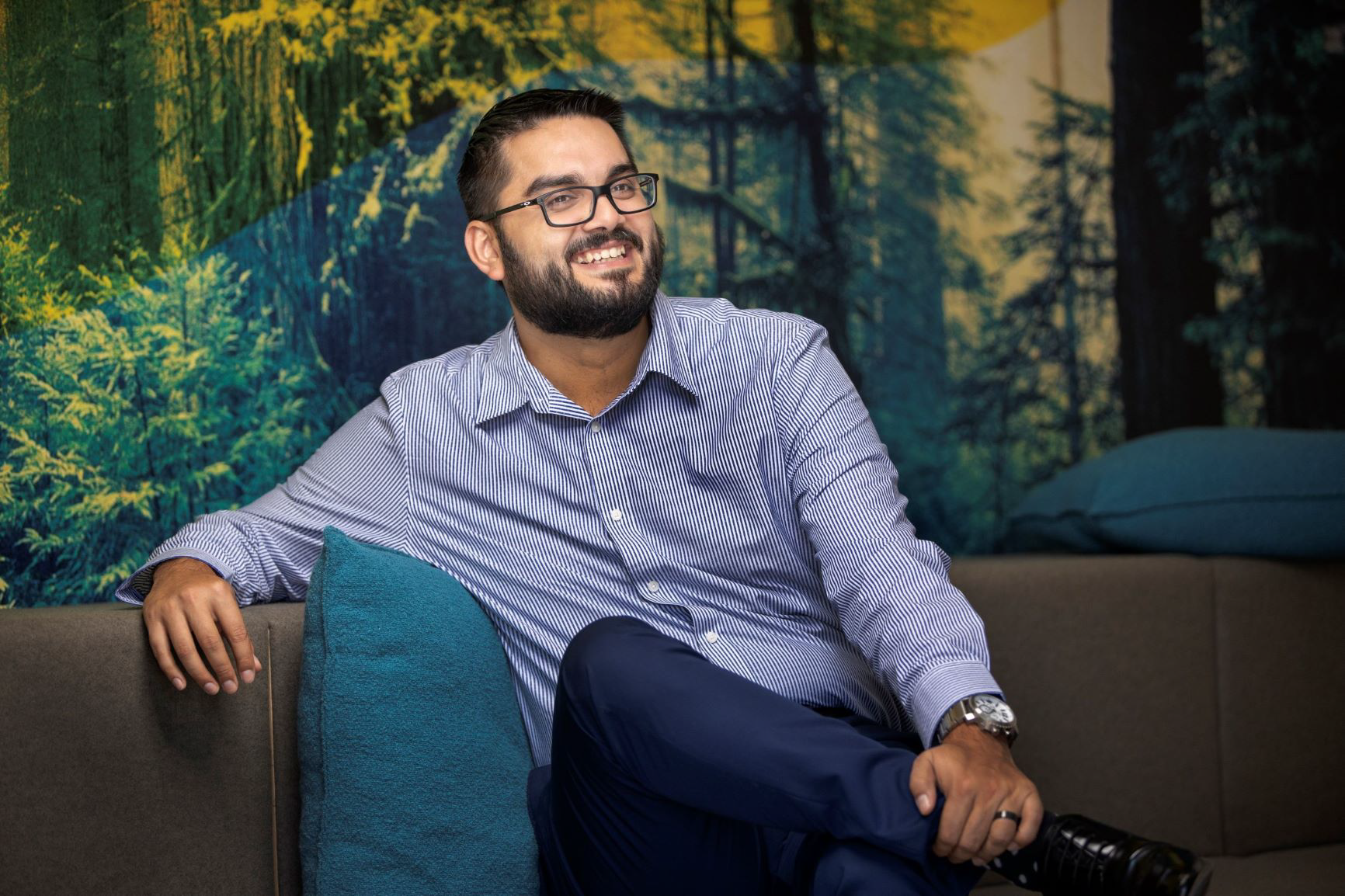
RETHINKING THE WAY WE THINK
Powering the planet with cleaner energy is a huge job. It takes curious minds and people who are always willing to ask, “What if?” At SCE, we know that revolutionizing the industry begins with revolutionizing the way we think and act. That’s why we’re committed to building a culture of Continuous Improvement—an environment that inspires transformation and helps us all to make a difference.
BECOMING BETTER
Continuous Improvement (CI) is more than a goal. It’s an entire set of capabilities, processes, organizational structure and a cultural shift here at Southern California Edison. CI helps develop problem solving. It builds leadership skill sets. And it improves performance in our organization in a systematic and sustainable way.
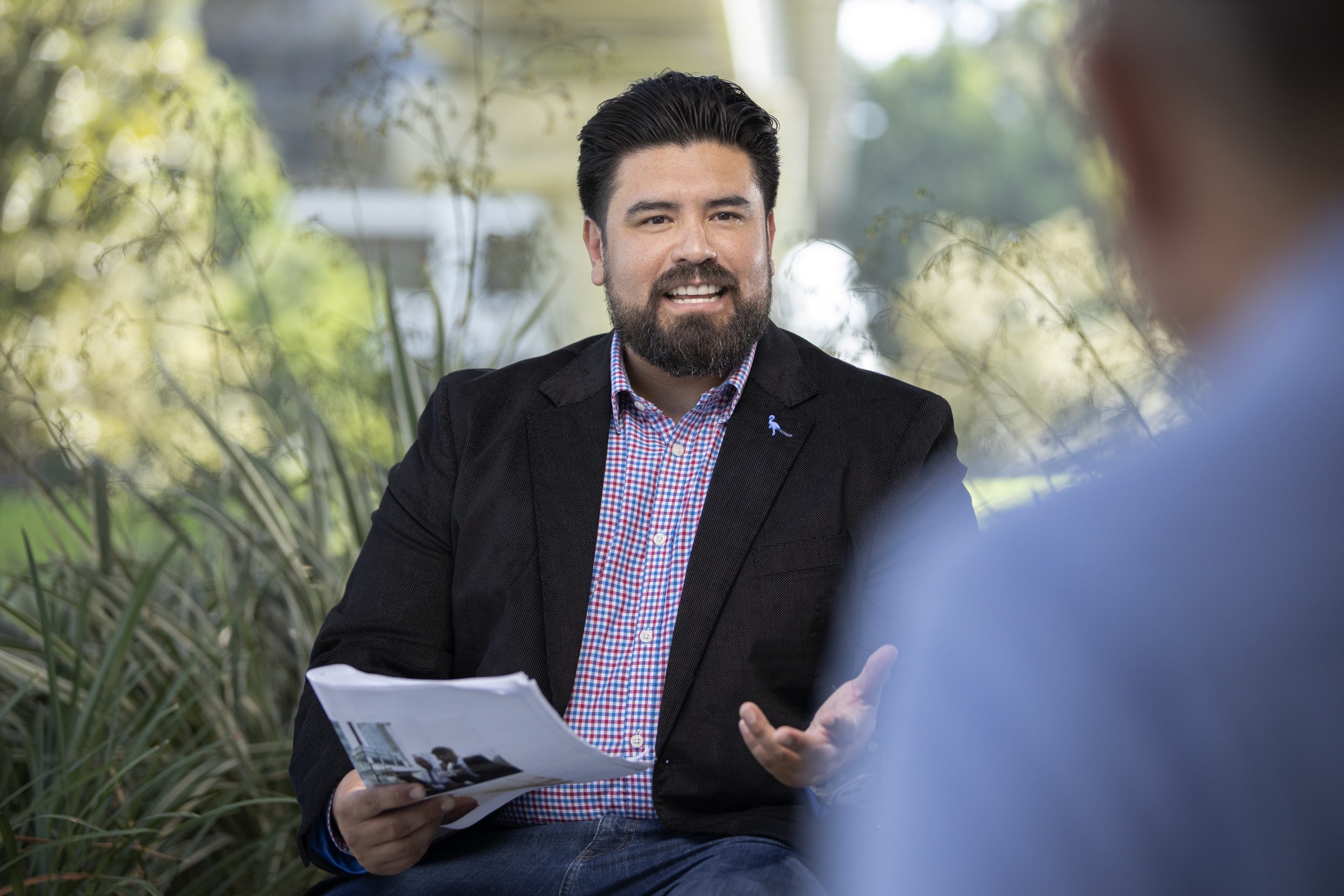
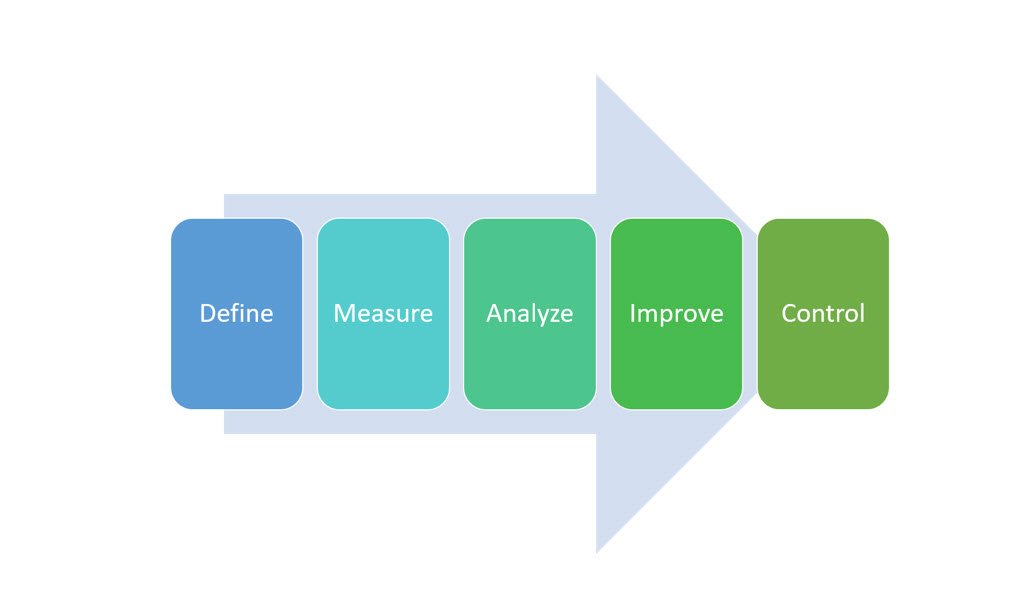
A NEW STANDARD
We’re using Lean Six Sigma (LSS) as our standard, and everyone will play a role. Our Continuous Improvement approach is aligned with our overall strategy and designed to empower SCE employees to solve problems and make process improvements as a part of their regular activities. There are so many ways to join in:
- Powerful tools and templates on our intranet
- Engaging training seminars
- CI events
- LSS classes where you can earn LSS certifications
OUR STORIES OF SUCCESS
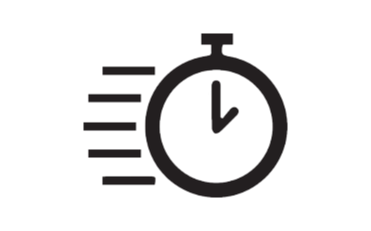
Minute Map
Work orders’ map corrections were taking 10 minutes to process. Multiply that by a few thousand work orders and it adds up! Our team was able to reduce it to 1.5 minutes, saving approximately 500 hours each year.
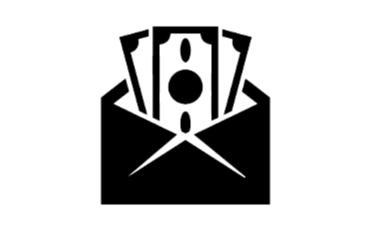
Rebate Wait
After a customer’s final inspection, rebate checks were taking an average of 90 days to process, understandably resulting in complaints. Our team was able to reduce that timeframe by 24 days.
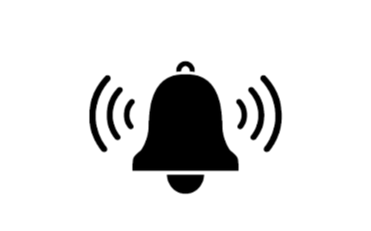
ID Me
Identifying Public Safety Power Shutoff (PSPS) customers was taking about a full day, delaying our ability to notify them of a PSPS event. Our team was able to reduce that identification process down to 10 minutes.